- Lean Management – Von Verschwendung zu Perfektion
- Lean Six Sigma in der Finanzbranche
- (Statisches) Weighted Scoring Model
- Histogramm
- FMEA
- Zusammenführung von Six Sigma und professionellem Projektmanagement
- Quality Function Deployment
- Was ist Lean?
- Kausalzusammenhäng(e und Korrelationen
- Pareto-Analyse
- Die Six-Sigma-Erfolgsgeschichte
- Voice of Customer
- DMAIC
- Brainstorming
- SIPOC
- ISO-Zertifizierungen im internationalen Vergleich
Lean Management – Von Verschwendung zu Perfektion
“The most dangerous kind of waste is the waste we do not recognize.” – Shigeo Shingo, Ingenieur und Mitentwickler des Toyota-Produktionssystems
Anfang der 90er Jahre revolutionierte die Firma Toyota die Automobilbranche. Mit der Veröffentlichung des Toyota-Produktionssystems legte Toyota den Grundstein für das moderne Prozess- und Qualitätsmanagements. Ziel war es, die Produktion vollständig auf die Bedürfnisse des Kunden auszurichten und dabei jegliche Verschwendung entlang der Wertschöpfungskette zu eliminieren. Im Laufe der Jahre wurde das Konzept der schlanken Produktion immer weiter verallgemeinert und der Begriff des Lean Managements wurde implementiert.
“There are so many men who can figure costs, and so few who can measure values.” – unbekannter Autor
Lean Management hat längst nicht mehr die fertigende Industrie mit dem Schwerpunkt Automobilindustrie im Fokus, sondern sie hat sich zu einer Führungsphilosophie entwickelt. Über alle Unternehmensprozesse hinweg soll jegliche Form von Verschwendung vermieden, die Kosten unnötiger Fehler minimiert und gleichzeitig ein Bestreben nach bestmöglicher Qualität implementiert werden.
Als Lean Management wird längst eine permanente, konsequente und integrierte Anwendung eines ganzen Bündels von Prinzipien, Methoden und Maßnahmen zur effektiven und effizienten Planung, Gestaltung und Kontrolle entlang der gesamten Wertschöpfungskette von Gütern und Dienstleistungen verstanden. Vor allem implementiert Lean Management eine Organisations- und Führungsphilosophie, auf die das gesamte Unternehmen ausgerichtet wird.
Beispielhafte Gegenüberstellung des Lean Managements mit traditioneller Führungsphilosophie:
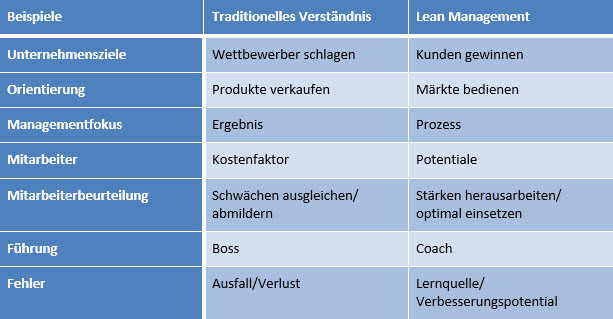
Ausgehend von dem Gedanken, dass in einer Unternehmung nur die Prozesse erhalten bleiben sollen, die zur Leistungserzielung und somit zur Wertschöpfung notwendig sind, kann die Qualität der angebotenen Leistungen nachhaltig gesteigert und die Kosten stark gesenkt werden. Die Verschlankung der Prozesse ist dabei vor allem durch den Abbau von Hierarchien zu erreichen, um die Nachteile bestehender Organisationsmuster wie z.B. der Matrixorganisation auszugleichen. Zu diesem Zweck müssen entsprechende Arbeitsphilosophien entwickelt werden. Lean Management lässt sich nicht durch die bloße Anwendung einzelner Tools und Techniken umsetzen, sondern nur durch die konsequente Ausrichtung aller Unternehmensprozesse an den Prinzipien des Lean Managements.nach oben
Lean Six Sigma in der Finanzbranche
Anfang der 90er Jahre wurde unter dem Titel „Die zweite Revolution in der Automobilindustrie“ ein Konzept entwickelt, das Effizienz und Qualität von Entwicklungs- und Produktionssystemen steigern sollte. Ziel war es, schlanke Produktionsprozesse („lean production“) in der Automobilindustrie zu etablieren und dabei vor allem die Prinzipien einer schlanken Organisation in den Vordergrund zu stellen. Doch dieser Fokus verschob sich bald. Aus dem Begriff der „Lean Production“ wurde „Lean Management“, der eine Führungsphilosophie definierte, die weit über die Grenzen der Automobilindustrie und ihrer Zulieferer von Managern in allen Branchen adaptiert wurde. 2002 wurde dann das moderne Lean Management mit dem Six Sigma-Konzept kombiniert.
Lean Six Sigma gilt heute als eine der effizientesten Management-Methoden. Ein standardisierter Verbesserungsprozess nach dem DMAIC-Zyklus (Define – Measure – Analyze – Improve – Control), die Vermeidung von Verschwendung entlang einer Prozesskette, die statistische Optimierung von Prozessen auf ein Fehlerniveau nahe Null und die zielgerichtete Ausbildung des Projektteams entsprechend der Lean Six-Sigma-Methode sind nur einige Vorteile, die dieses Management-Konzept bietet.
Längst ist Lean Six Sigma nicht mehr nur auf Produktionsprozesse beschränkt, sondern kann genutzt werden, um jede Form von Prozessen zu optimieren. Auch in der Finanzindustrie ist Lean Six Sigma mittlerweile ein wichtiges Thema. Mit Hilfe der Lean-Methode werden drei zentrale Hemmfaktoren systematisch identifiziert und reduziert:
1) Inflexibilität (Unfähigkeit, dem Kunden zum gewünschten Termin und in der richtigen Menge genau das zu liefern, was er bestellt hat)
2) Verschwendung (Nutzung von Ressourcen für Tätigkeiten, die keinen Mehrwert für den Kunden schaffen und nicht notwendig sind, z.B. „gold plating“ bzw. Übererfüllung)
3) Variabilität (Änderungen von Qualität und Durchlaufzeit aufgrund von Unterschieden in diversen Faktoren, z.B. Mensch, Prozesse)
Zur Umsetzung von Lean Six Sigma in der Finanzbranche lassen sich vier Hebel herausarbeiten, die unterschiedliche Maßnahmen umfassen und Schwachstellen im Prozessdesign ausgleichen sollen.
1. Einführung eines systematischen Team- und Leistungsmanagements
Im Bereich des Teammanagements steht die Verbreitung von Fähigkeiten im Vordergrund, um ein optimales Kapazitätsmanagement zu erfüllen (Multi-Skilling). Ziel ist die Einteilung sehr kleiner und systemspezialisierter Teams innerhalb einzelner Gruppen. Um eine konstante Leistungserfassung zu ermöglichen, ist außerdem die Einführung eines stringenten Leistungsmanagements auf Basis von Kennzahlen notwendig.
2. Stärkung der Zusammenarbeit zwischen Finanzbuchhaltung und IT
Ein aufwendiger und starrer Budgetierungsprozess basiert auf stabilen Anforderungen, die sich aber häufig verändern und selten über einen längeren Zeitraum stabil sind. Eine optimierte Budgetsteuerung soll dabei zur Verbesserung einer systematischen Projekt-Portfolio-Steuerung führen. Die Einführung technischer Hilfsmittel zur Verbesserung der Kommunikation und der Zusammenarbeit virtueller Teams ist eine zentrale IT-Herausforderung. Räumliche Trennung erschwert häufig die Zusammenarbeit vor allem dann, wenn keine geeigneten technischen Hilfsmittel zur Verfügung stehen. Außerdem sieht dieser Hebel die Einführung einer expliziten Projektorganisation in der Finanzbuchhaltung sowie eine übergreifende Kapazitätsplanung vor.
3. Ausbau agiler Entwicklungsmethoden
Vor allem lange Entscheidungsprozesse bei Fachkonzeptionsanfragen können den Projektstart verzögern. Die Einführung von Best-Practice-Agile Entwicklungsmethoden kann diesem Problem entgegenwirken. So lässt sich beispielsweise die Scrum-Methode weitgehend anpassen und in eine vorhandene Organisationsstruktur einbinden. Auch eine Implementierung von Standardmethoden bei der Aufwandsschätzung von Projekten können Verzögerungen des Projektstarts verhindern. So können verbindliche Aufwandsschätzung trotz ungenügender Information sehr früh beauftragt werden. Jedoch ist es notwendig, wesentliche Änderungen im Projektverlauf vor allem aufgrund regulatorischer Anforderungen, flexibel und schnell integrieren zu können.
4. Optimierung der Zusammenarbeit mit internen Dienstleistern
Häufig sind vor allem die interne Logistik und IT-Dienstleistungen zu langsam, intransparent, zu komplex und nicht flexibel genug, sodass sich unnötige Verzögerungen und somit Verschwendung ergeben. Mittels der Implementierung messbarer Qualitätsstandards und kürzerer Rückmeldezeiten lassen sich diese Schwachstellen ausgleichen. Dabei kann auch die Vereinfachung von Vorgaben z.B. durch den Einsatz von Checklisten hilfreich sein, Prozesse effizienter und vor allem transparenter zu gestalten.
Implementierung von Lean Six Sigma – Die nächsten Schritte
Die Einführung von Lean Six Sigma ist nur im Dialog zwischen Management und Team möglich. Ein Lean Six Sigma Kernteam sollte alle notwendigen Schritte unterstützen und begleiten. Innerhalb bestimmter Gruppen sollten unter der Führung eines Gruppenleiters Basis-Informationen erhoben werden und darauf aufbauend auch „Mini“-Diagnosen über die Fähigkeit der Prozesse gestellt werden. Auch eine Datenerhebung zur Nachfrageanalyse beinhaltet wertvolle Informationen über die Ansprüche, die an einen Prozess gestellt werden. Der Implementierungsplan geplanter Maßnahmen sollte allen Beteiligten kommuniziert werden. Hierbei ist ein Kick-Off-Meeting mit der gesamten Gruppe und möglicherweise weiterer Beteiligter unerlässlich.nach oben
(Statisches) Weighted Scoring Model
Das „Weighted Scoring Model“ ist eine Messmethode zum Vergleich unterschiedlicher Projekt- oder Handlungsalternativen hinsichtlich verschiedener (gewichteter) Messgrößen.
Ablauf:
1) Definition von Bewertungskriterien (z.B. mögliche Rentabilität, finanzieller Aufwand)
2) Kriterien anhand ihrer Bedeutung gewichten (Summe der Gewichtungen = 100%)
3) Erfüllungsgrad der einzelnen Kriterien ermitteln (z.B. mögliche Rentabilität = 15.000€ oder 20 „Punkte“)
4) Gewichtete Bewertungen berechnen und für jede Projektalternative addieren
Ergebnis: Die Summe aller bewerteten Kriterien ergibt die Bewertung des Projektes, die dann mit der Summe der anderen Projekte verglichen werden kann.
Beispiel
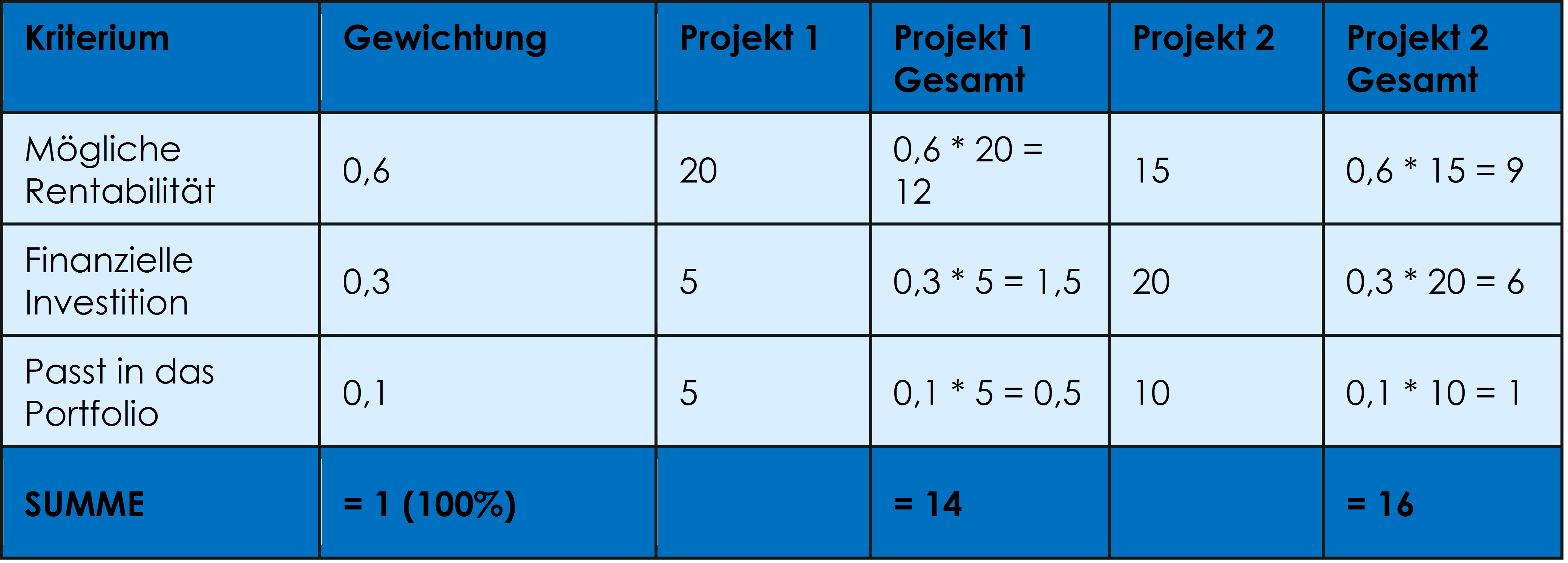
Ergebnis: Projekt 2 wird höher priorisiert / ausgewählt
Kritik und Erweiterungsmöglichkeit:Um eine echte Relevanz für tatsächliche Entscheidungen zu bilden, reicht oftmals eine statische Einschätzung möglicher Umweltzustände nicht aus. Einflussgrößen wie z.B. „Mögliche Rentabilität“ hängen von Inputfaktoren ab, welche ihrerseits zum Teil schwer abschätzbar sein können. Aus Erfahrungen der Vergangenheit kann man jedoch Aussage über eine zugehörige Wahrscheinlichkeitsfunktion treffen, nach der sich eine bestimmte Kennzahl in der Vergangenheit verhalten hat und in der Zukunft verhalten könnte. Dadurch kann ein „statisches Weighted Scoring Model” in ein “multivariates stochastisch-dynamisches Weighted Scoring Model“ erweitert werden. Eine anschließende Simulation mit hoher Iterationszahl ermöglicht somit eine wesentlich genauere (zum Teil sogar von der statischen Sicht deutlich abweichende) Einschätzung über die Vorteilhaftigkeit verschiedener Handlungsalternativen.nach oben
Histogramm
Ein Histogramm eignet sich dazu, bestimmte metrisch verteilte Merkmale einer Häufigkeitsverteilung grafisch darzustellen und anschließend unter Verwendung verschiedene Methoden zu analysieren. Für normalverteilte Zufallsgrößen ergibt sich dadurch die bekannte Gaußsche Glockenkurve. Die Fläche innerhalb eines Histogramms präsentiert 100 % aller gemessenen Merkmalsausprägungen. Somit wird es möglich, durch das Einsetzen von Unter- und Obergrenzen (UGW und OGW) Angaben über die Häufigkeit für das Eintreten eines Merkmals zu definieren. Daher kann diese Form der Darstellung auch als geschätzte Wahrscheinlichkeitsdichte einer Zufallsvariable (Ausprägung) bezeichnet werden.
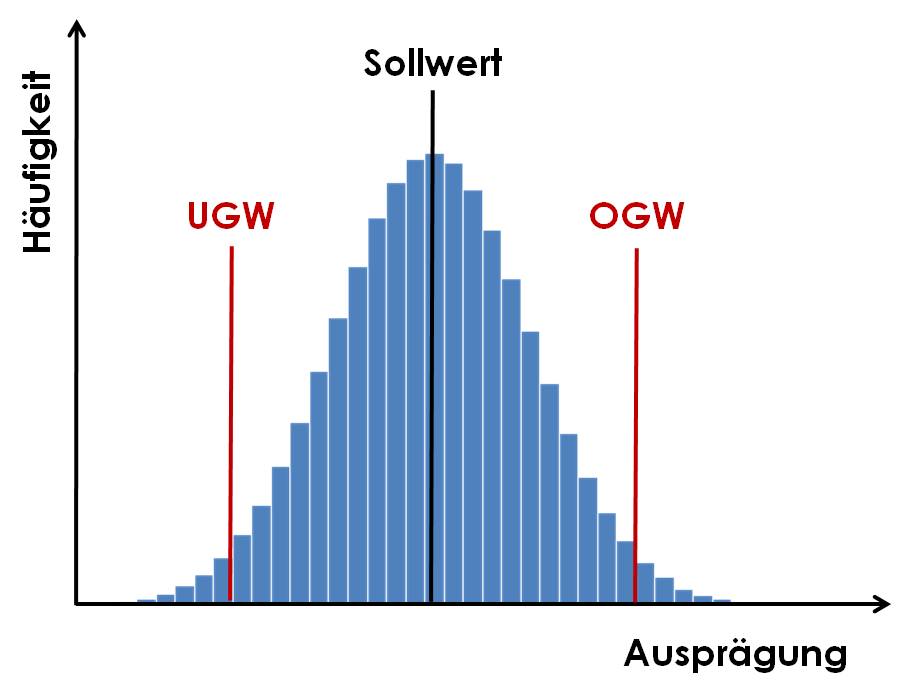
In der Praxis können mit solch einfachen Methoden schnell Aussagen darüber getroffen werden, mit welcher Wahrscheinlichkeit bestimmte Ereignisse eingetreten sind oder eintreten werden. Beispielsweise kann so der anfallende Ausschuss einer Produktion unter Vorgabe eines zu erfüllenden Qualitätsmerkmals (Sollwert) berechnet werden. Die „Breite“ des Histogramms gibt dabei einen Hinweise über die Standardabweichung der Inputdaten, d.h. wie weit die Werte um den gewünschten Sollwert streuen. Unternehmen können somit ihre Qualitätsversprechen statistisch überprüfen.
In der Realität wird es jedoch selten zu normalverteilten Messergebnissen kommen. Hier bieten Softwarelösungen wie z.B. Minitab, Excel oder @Risk Möglichkeiten, auf schnelle und Effektive Art und Weise Messwerte automatisch und für eine weitere Verwendung (z.B. für Reports) auszuwerten.nach oben
FMEA
Die Fehlermöglichkeits- und Einflussanalyse (kurz FMEA) ist eine Technik, um potentielle Schwachstellen in einem Prozess zu finden und folgt dabei dem Grundgedanken der vorsorgenden Fehlervermeidung anstatt einer nachsorgenden Fehlererkennung. Ziel ist es, anfallende Kontroll- und Fehlerbehebungskosten nachhaltig zu senken. Die FMEA bietet eine systematische Vorgehensweise, die schon in frühen Phasen der Produkt- und Prozessentwicklung innerhalb eines Produktlebenszyklus angewendet werden kann. Gerade in den frühen Phasen des Produktlebenszyklus sind die Kosten pro Fehler noch relativ gering (siehe Abbildung: Fehlerkostenentwicklung).
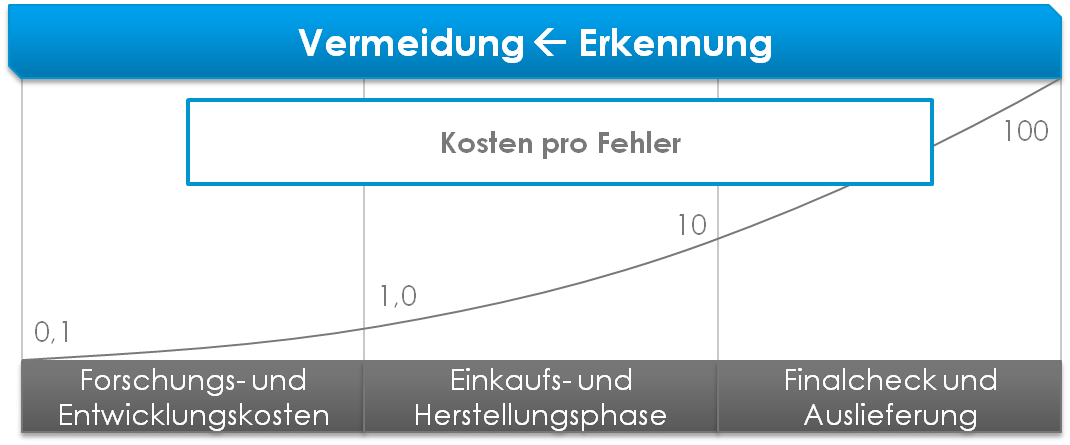
Abbildung: Fehlerkostenentwicklung
Innerhalb eines Six Sigma-Projektes wird die FMEA sowohl von Black Belts als auch von Green Belts durchgeführt und dient dazu, mögliche Fehler oder bereits vorhandene Fehler an einem Produkt oder in einem Prozess zu verhindern oder zu beseitigen.
Die FMEA umfasst folgende Maßnahmen:
– Eingrenzung und Strukturierung des zu betrachtenden Systems
– Definition von Funktionen der Strukturelemente
– Analyse potentieller Fehlerursachen, Fehlerarten und Fehlerfolgen
– Risikobeurteilung
– Maßnahmen/ Lösungsvorschläge für priorisierte Risiken
– Überwachung der Fehlervermeidungs- und Entdeckungsmaßnahmennach oben
Zusammenführung von Six Sigma und professionellem Projektmanagement
Um langfristig wettbewerbsfähig zu sein, müssen Unternehmen ihre Leistungen und ihre Produktion stetig verbessern und ausbauen. Produkte und Services sollen günstiger werden, besser verfügbar sein und den Qualitätsanforderungen der Kunden entsprechen. Für das Projektportfolio bedeutet dies, dass Projekte mit dem Ziel umgesetzt werden, zum einen Kosten zu reduzieren und zum anderen neue Umsätze und Gewinne zu realisieren .
Das Project Management Institute (PMI) auf der einen Seite stellt einen umfangreichen Standard zur Verfügung, nach denen Projekte konzipiert, umgesetzt, kontrolliert und letztendlich (erfolgreich) geschlossen werden sollen, konzentriert sich dabei aber auf die Eigenschaften und den Ablauf eines Projektes. Eine klare Prozessstruktur ermöglicht ein hohes Maß an Projektkontrolle und bildet so die Grundlage für den erfolgreichen Abschluss eines Projektes.
Die Six Sigma-Methodik auf der anderen Seite stellt Tools und Konzepte zur Verfügung, mit denen sich im Rahmen eines kontinuierlichen Verbesserungsprozesses Fehler nahezu vermeiden lassen und sich so die Qualität der Leistung nachhaltig steigern lässt. Ein strukturiertes Vorgehen (DMAIC) und statistische Prozesskontrolle bilden das Zentrum eines Six Sigma-Projektes. Ihren Ursprung hat die Six Sigma-Methodik in der Produktion, ist jedoch nicht auf produzierende Prozesse beschränkt. Grundsätzlich gilt, dass sich jeder Prozess, der eine Handlung beinhaltet, Kontrolle verlangt und „in Bewegung“ ist, mittels des Six Sigma-Konzeptes verbessern lässt.
Ziel ist es daher, beide Konzepte miteinander zu verbinden und ihre jeweiligen Stärken zu nutzen. Durch die erhöhte Prozesskontrolle des Projektmanagements nach PMI® und der Strategie der statistischen Fehlerreduzierung ergibt sich so ein konsistenter, planbarer und kontrollierter Prozess der kontinuierlichen Verbesserung und systematischen Fehlervermeidung.
Schon bei der Entwicklung eines Projektes können Konzepte der Six Sigma-Methodik angewandt werden. Beispielsweise dienen bei der Problemdefinition Six Sigma-Tools dazu, mögliche Fehler zu reduzieren, die durch falsche oder unterschiedliche Vorstellungen über das Problem entstehen können. Aber auch bei der Bewertung des Problems lassen sich verschiedene Werkzeuge (Gauge R&R, FMEA, Control Charts) anwenden. Wie sich über die verschiedenen Projektphasen Six Sigma und Projektmanagement ergänzen, ist in der Abbildung „Integration von Six Sigma und Projektmanagement“ dargestellt.
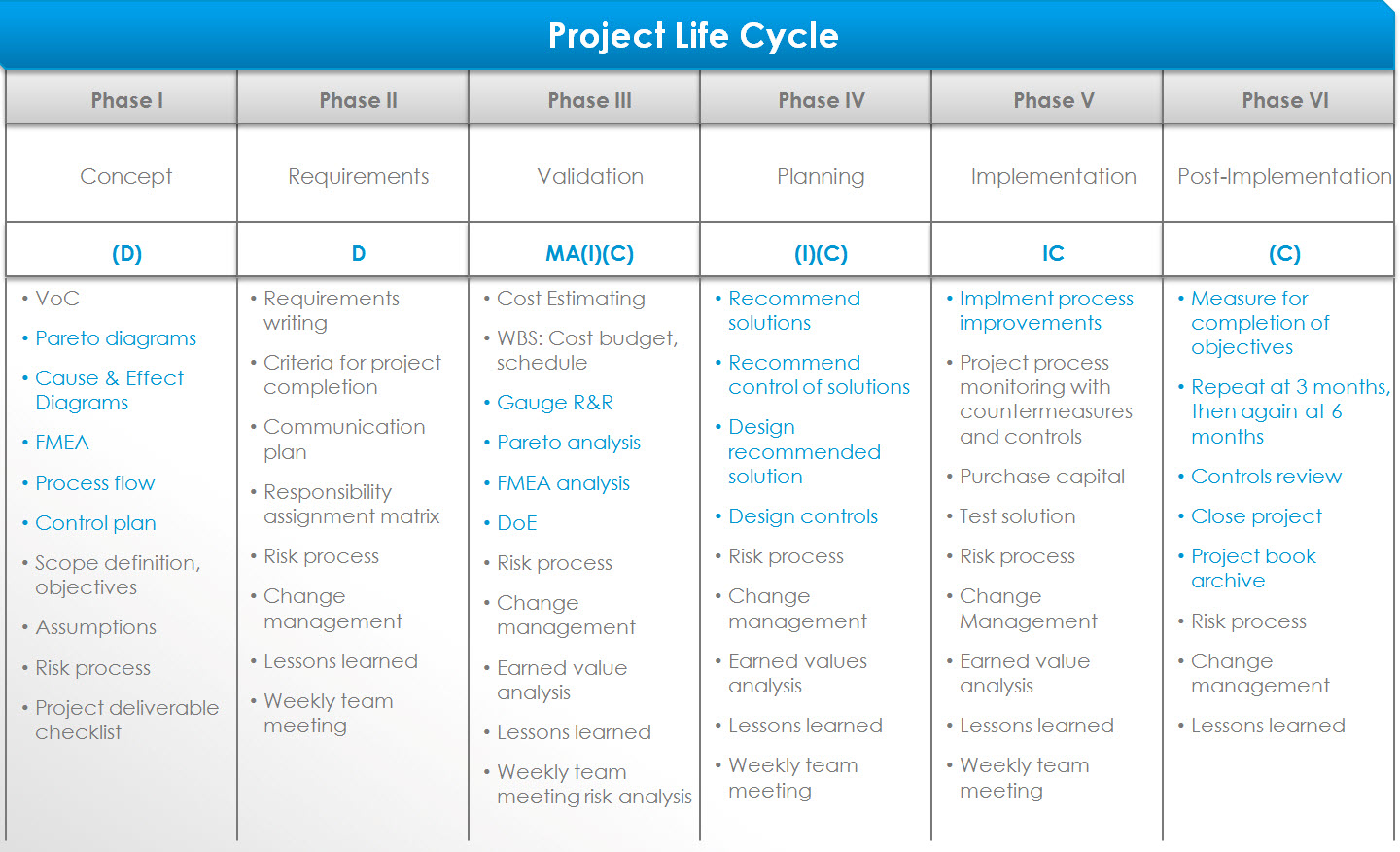
Abbildung: Integration von Six Sigma und Projektmanagement
Quelle: http://www.pmi.org/Knowledge-Center/~/media/PDF/Knowledge-Shelf/Zucker-2012.ashx, abgerufen am 13.09.2013nach oben
Quality Function Deployment
Quality Function Deployment ist eine umfassende Planungs- und Kommunikationsmethode, welche dazu dient, Ressourcen eines Unternehmens zusammenzuführen und zu koordinieren. Ziel der Anwendung der Methode ist die Entwicklung, Herstellung und Vermarktung von Produkten und/oder Dienstleistungen, die einen echten Kundennutzen aufweisen. Dabei werden Markt- und Kundenanforderungen in unternehmensinterne Anforderungen übertragen und diese in jeder Phase und jedem Bereich der Leistungserstellung berücksichtigt.
Die zentrale Herausforderung ist die Aufnahme und Umwandlung der Kundenstimmen (Voice of Customer) in unternehmensinterne Spezifikationen der Leistung. Es muss dabei eine umfangreiche Erhebung der Kundenstimmen vorgenommen werden, was viel Zeit und ebenfalls Kosten in Anspruch nimmt. Wenn die Anforderungen des Kunden an die Leistung bekannt sind, können die Kundenwünsche in die eigene Leistung überführt werden – hier gilt: je detaillierter und präziser die Anforderungen aufgefasst wurden, desto besser ist die Übersetzung in die eigene Leistung.
Um die Beziehung zwischen den Kundenanforderungen und Leistungsmerkmalen darzustellen wird das House of Quality verwendet. Dieses wird in sechs Schritten erstellt:
1. Erhebung der Kundenanforderungen und Gewichtung der Anforderungen aus der Sicht des Kunden.
2. Beurteilung der Wettbewerbsleistung seitens des Kunden für einen Konkurrenzvergleich. Zudem kann durch die Gewichtung der Kundenanforderung eine Priorisierung erstellt werden.
3. Umsetzung der Kundenanforderung in technische Merkmale. Für jede Kundenanforderung werden an der Gesamtleistung messbare und kontrollierbare technische Merkmale ermittelt.
4. Verknüpfung von Qualitätsmerkmalen der Leistung mit den resultierenden Erfüllungsgraden für die Kundenanforderung.
5. Technische Bedeutung der Qualitätsmerkmale errechnet sich aus dem Produkt der Prioritäten, der Kundenanforderung und den entsprechenden Spalten der Qualitätsmerkmale in der Beziehungsmatrix.
6. Das ‚Dach‘ bildet die Korrelationsmatrix und dient zur Verdeutlichung von Zielkonflikten. Diese entstehen durch positive und negative Wechselwirkungen einzelner Qualitätsmerkmale.
Abschließend wird eine grafische Abbildung erstellt, um einen Überblick über die Beziehungen zwischen Anforderungen und Leistungsmerkmalen zu erhalten:
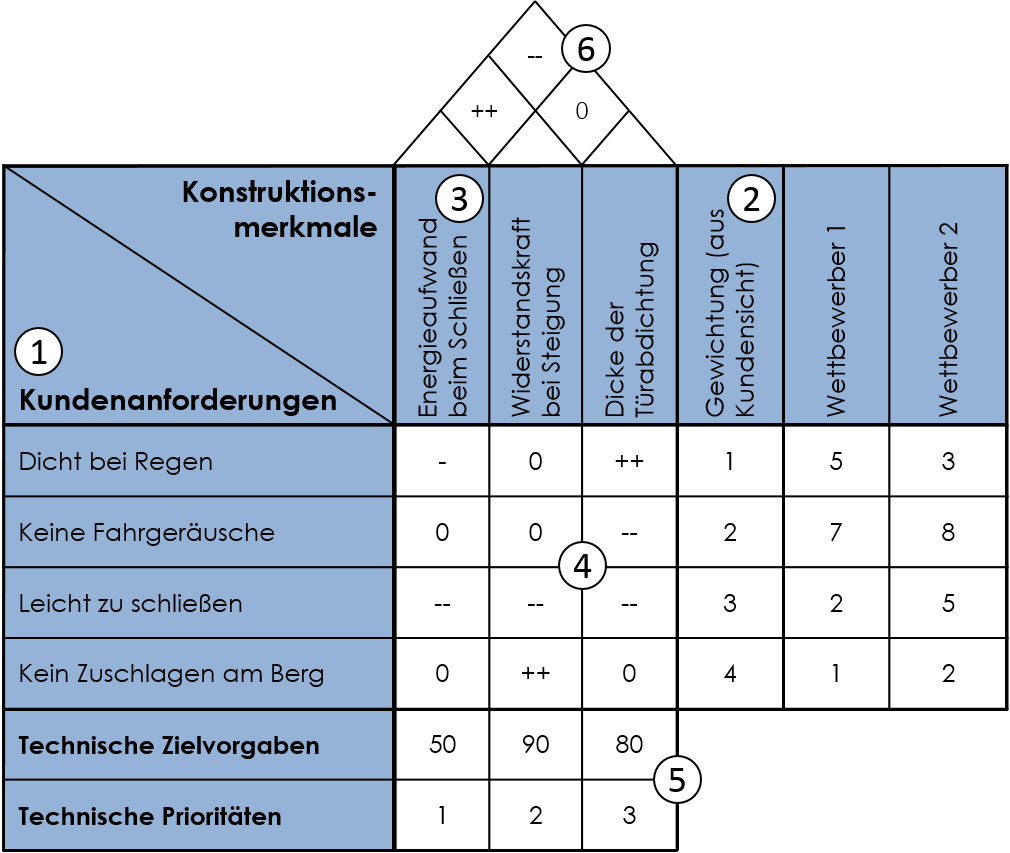
Abbildung: House of Qualitynach oben
Was ist Lean?
Zu allererst stellt sich die Frage was dieses englische Wort „lean“ eigentlich bedeutet. Eine direkte Übersetzung ins deutsche gibt es nicht, man findet dennoch Synonyme wie mager, arm, dünn oder knapp, welche erste Hinweise auf die Bedeutung im Bezug auf Produktions- und Prozessmanagement geben. Ob „lean“ wohl etwas damit zu tun hat die Produktion zu kürzen oder doch eher die Prozesse auszudünnen ist jedoch zu diesem Zeitpunkt noch unklar.
Um die eigentlichen Ziele des Lean Management etwas deutlicher zu machen muss man sich die Entstehung dieses Prozessmanagementsystems anschauen. Die Begriffe „Lean Production“, „Lean Thinking“ und „Lean Enterprise“ entstammen von ihren Wurzeln her dem sogenannten Toyota Production System. Dieses System ist nicht nur eine Sammlung von Tools, sondern bietet Ansätze und Methoden, die im weitesten Sinne eine konsequente Vermeidung von Verschwendung beinhalten. Das Toyota-Production-System wurde federführend von Taiichi Ohno (1912-1990) in der Zeit nach dem Zweiten Weltkrieg bei der Toyota Motor Corporation entwickelt und verhalf dem Konzern in den folgenden Jahrzehnten zu stetigem Wachstum und einem hohen Qualitätsniveau. Als Grundlage für die Arbeit von Ohno verwendete er das von Henry Ford und Frederick Taylor entwickelte System der Massenproduktion.
Nun haben wir uns die Geschichte des Lean Managements angeschaut, doch worin liegt eigentlich das Ziel dieser Methode? Die wichtigsten Zielgrößen lassen sich wie folgt definieren: größtmöglicher Durchsatz; maximale Auslastung der Anlagen; maximale Auslastung der Arbeitskräfte; geringste Stückkosten; große Losgrößen und seltenes Umrüsten von Anlagen. Lean-Management bietet zahlreiche Methoden und gibt Anweisungen wie man diese Ziele erreichen kann. Viele dieser basieren abermals auf den Theorien von Henry Ford und Frederick Taylor.
Dieses Managementsystem bringt allerdings nicht nur positive Aspekte mit sich. Durch die Umstellung der Prozesse kann es auch zu Problemen kommen, wie zum Beispiel hohe Durchlaufzeiten oder lange Transportwege. Ein weiteres Problem kann durch den größtmöglichen Durchsatz entstehen: Warteschlangen an Engpässen. Fehlerhafte Einheiten könnten erst zu spät entdeckt werden, da der Zeitdruck in den einzelnen Arbeitsprozessen, beispielsweise durch ein „Just-In-Time“ Produktions-verfahren, forciert ist. Durch Einführung des Lean Managements muss verstärkt auf mögliche Probleme bei der Umsetzung geachtet werden, da die Optimierung der Prozesse großes Fehlerpotenzial bietet.
Der gegenwärtige Zustand des Prozessmanagements in Unternehmen bietet durchaus Potenzial für Verbesserung. Die meisten Prozesse sind nicht „lean“, d.h. sie haben eine Prozesszykluseffizienz von kleiner 10% (wertschöpfende Zeit / Gesamtdurchlaufzeit). Primäres Ziel ist die Reduzierung der Prozess-Bearbeitungszeit, aber auch die Anzahl der Einheiten in den Prozessen. Nach dem Pareto Prinzip rufen 20% der Ursachen 80% der Verzögerungen hervor, somit bieten scheinbar kleine Änderungen ein extrem großes Verbesserungspotenzial. Sämtliche Abläufe müssen datenbasiert gestaltet werden, da unsichtbare Leistungsanteile nicht verbessert werden können. Zur Reduzierung der Streuung und der Durchlaufzeit sollten Prozesse vorgezogen und nicht hinten angeschoben werden. In nahezu jeder Branche der Produktion, bzw. des Managements gibt es diese signifikanten Verbesserungsmöglichkeiten, welche sich langfristig extrem positiv auf die Wettbewerbsfähigkeit der Unternehmen auswirken.nach oben
Kausalzusammenhänge und Korrelationen
Es ist sicher interessant zu erfahren, wie groß die Maschinen für die Autoproduktion sind und die relative Verteilung auf die einzelnen Marken aussieht. Noch interessanter sind jedoch kausale Zusammenhänge. In unserem Beispiel würde dies bedeuten, dass man die Größe der Maschinen mit der Qualität des Autos in Verbindung setzt und somit auf einen Zusammenhang überprüft.
Einen solchen Zusammenhang nennt man in der Statistik eine Korrelation. Der mathematische Zusammenhang zwischen zwei Variablen kann dabei positiv oder negativ sein; bei einer positiven Korrelation steigt der Wert einer Variablen mit dem Zuwachs der anderen. In unserem Beispiel wäre eine positive Korrelation, dass Marken mit größeren Maschinen qualitativ hochwertigere Autos produzieren. Eine negative Korrelation wäre, dass Marken mit großen Maschinen qualitativ schlechtere Autos produzieren. Dritte Möglichkeit ist, dass kein Zusammenhang zwischen der Größe der Maschinen und Qualität der Autos besteht. In unserem Beispiel die wahrscheinlichste Variante.
Nehmen wir nun an, eine statistische Analyse ergibt, dass zwei Variablen sehr stark miteinander korrelieren. Heißt dies nun auch zwingend, dass diese beiden Variablen einander tatsächlich beeinflussen? Der Schluss liegt nahe, ist aber falsch. Die tatsächliche Ursache kann beispielsweise durch eine dritte Variable bedingt sein, die auf beide Variablen Auswirkungen hat. Um auf unser Beispiel zurückzukommen: Nehmen wir an, es existiert eine positive Korrelation zwischen Größe der Maschinen und Qualität des Autos, d.h. je größer die Maschine, desto besser das Auto. Nun könnte man annehmen, dass alle Autos die von einer großen Maschine gefertigt wurden besser sind als die, die von einer kleinen Maschine gefertigt wurden. Dies ist durchaus denkbar, aber ein anderer Grund ist deutlich wahrscheinlicher. Der Durchschnittspreis von Autos, die durch große Maschinen gefertigt wurden, ist deutlich hohen als der Preis der Autos, die mit kleinen Maschinen gefertigt wurde. Wenn ein Auto mehr Geld kostet, kann auch mehr Geld in die Maschinen gesteckt werden. Wirklich beweisen lässt sich eine Kausalität aber auch zwischen Preis des Autos und Maschinengröße nicht, dafür sind die Erhebungen nicht geeignet. Sie können lediglich ein stärkeres Indiz dafür liefern.
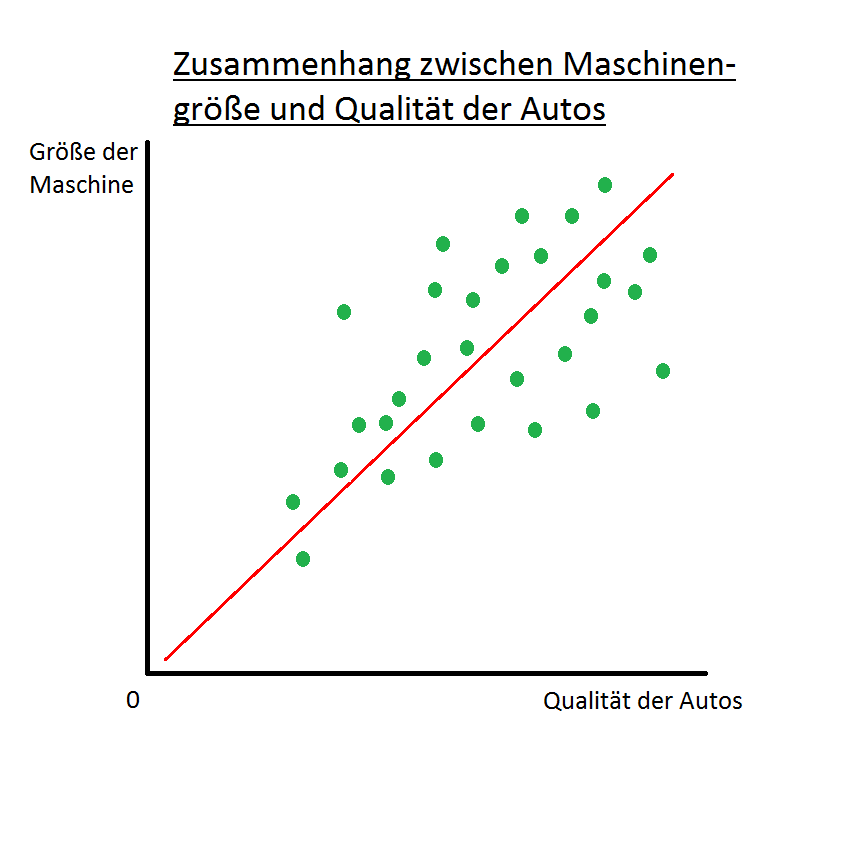
Pareto-Analyse
Die Pareto-Analyse ist ein elementares Six-Sigma Tool und basiert auf den Theorien des italienischen Ökonomien Vilfredo Pareto (1848-1923). Die Analyse hilft, das Wesentliche vom Unwesentlichen zu unterscheiden. Sie dient der Trennung der wenigen wichtigen Einflussgrößen von den vielen unwichtigen hinsichtlich der Gesamtwirkung und ebnet den Weg für gezielte Einleitung von Fehlerbehebungsmaßnahmen im Unternehmen. Im Bereich Six-Sigma wird die Pareto Analyse eingesetzt, um Fehlerarten zu definieren und dann die Fehlerhäufigkeit in Prozent zu ermitteln. Anhand dieser Prozentzahlen entsteht eine Rangliste, welche die Signifikanz der einzelnen Fehler im Bezug zu den Gesamtkosten der Fehlerbehebung aufzeigt.
Das Paretoprinzip, nach dem die meisten Auswirkungen eines Problems (80%) häufig nur auf eine kleine Anzahl von Ursachen (20%) zurückzuführen sind, ist die Grundlage der Analyse. Im Bereich Six-Sigma ist es wichtig diese 20% zu determinieren und gezielt zu versuchen gegen diese „Hauptfehlerquellen“ vorzugehen. Die Ergebnisse der Analyse verdeutlichen außerdem welche Ursachen bereits in einem guten Stand sind und kaum oder gar keine Fehlerbehebungsmaßnahmen benötigen. Wenn diese Bereiche erst einmal determiniert sind kann man schnell und effektiv die Gesamtkosten zur Fehlerbehebung reduzieren.
Das Diagramm zeigt ein Beispiel von Fehlerarten und die dazugehörigen Kosten zur Reparatur von Fahrrädern. Es wird auf einen Blick deutlich welche Fehlerquellen signifikant und welche zu vernachlässigen sind. Wie im Pareto Prinzip theoretisch dargestellt wird, kann man in dem Beispiel praktisch erkennen, dass ein kleiner Teil der Fehlerarten (Schaltung und Tretlager) einen großen, prozentualen Anteil (73%) an den Gesamtfehlerkosten haben. Der Fokus bei einem Fahrradhersteller sollte also mehr auf das Qualitätsmanagement von der Schaltung und vom Tretlager liegen.
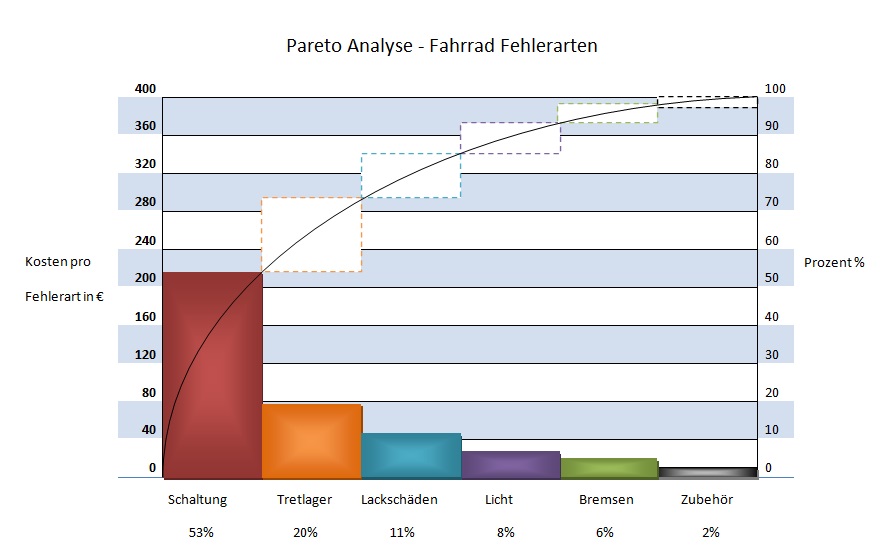
Die Six-Sigma-Erfolgsgeschichte
Die Grundlagen für Six Sigma sind den Theorien des deutschen Mathematiker und Astronom Carl Friedrich Gauß (1777-1855) zu entnehmen. Die von Gauß erfundene Normalverteilung ist ein wichtiger Typ der stetigen Wahrscheinlichkeitsverteilung und bildet zugleich die Grundlage für Six Sigma. Die Maßeinheit zur Bestimmung der Abweichung vom Mittelwert ist Sigma. Je höher der Sigma-Wert, desto mehr Wahrscheinlichkeiten sind abgedeckt und desto geringer ist die Fehlerwahrscheinlichkeit. Ein marktüblicher Standard beim Qualitätsmanagement sind 3 Sigma, das bedeutet eine Fehlerwahrscheinlichkeit von ca. 0,27%. Dieser Wert erscheint verschwindend gering, aber für Unternehmen wie die Deutsche Post, die täglich rund 72 Millionen Briefe verschickt, ist selbst das zu hoch.
Motorola nutzte diese Theorie als erstes Unternehmen, um in den achtziger Jahren ein unternehmensweites Qualitätsmanagement mit dem Namen „Six Sigma“ einzuführen. Um die Fehlerwahrscheinlichkeit zu reduzieren, hat Motorola die Varianz der einzelnen Produktionsprozesse drastisch verringert. Durch diese Standardisierung wurden Prozesse transparenter und messbarer. Motorola hat Teamarbeit, Transparenz und Messbarkeit als die Basis für eine unternehmensweite Ausrichtung auf den Kunden deklariert. Mit diesen Leitzielen und den weltweit einheitlichen Standards führte Motorola ein revolutionäres Qualitätsmanagement ein.
Zum globalen Durchbruch von Six Sigma musste ein noch einflussreicherer Konzern her. Die amerikanische Management-Ikone Jack Welch nutzte das von Motorola patentierte Verfahren und krempelte General Electics radikal um. Mit flächendeckenden Schulungsmaßnahmen und Beförderungen nur durch Six-Sigma-Erfolge trimmte er die Firma auf Kurs eines nahezu perfekten Qualitätsmanagements. Welch nutzte die bereits vorhandenen Theorien und verfeinerte sie genau auf die Bedürfnisse von GE. Durch diese Maßnahmen hatte Welch schon nach zwei Jahren in 1997 eine Verbesserung des Gewinns um 700$ Millionen zu verzeichnen. Dieses Erfolgsmodell bedeutete den endgültigen Durchbruch für Six Sigma. Heutzutage wird das Risiko, die hohen Startinvestitionen zu verlieren, durch das hohe Einspar-Potenzial mehr als kompensiert.nach oben
Voice of Customer
Das Konzept des „Voice of Customer“ (VoC) dient dazu, Kundenanforderungen in Zielgrößen umzuwandeln und schlägt somit eine Brücke zwischen einem häufig nur verbal geäußertem Kundenproblem und konkreten Maßnahmen zur Lösung des Problems. Haben beispielsweise Kunden das Problem, dass das Produkt „nur schwer zu bedienen“ ist, kann eine daraus abgeleitete Zielgröße sein, die „Beschriftungen auf dem Produkt zu vergrößern“.
Besonders wichtig ist dieses Werkzeug in der „Define“-Phase eines Six-Sigma-Verbesserungsprojekts. Eine schlechte Ergebnisqualität kommt häufig dadurch zustande, dass das Ergebnis von den Erwartungen des Kunden abweicht. Durch die VoC-Methode kann sichergestellt werden, dass sich Erwartungen des Kunden mit dem Projektergebnis decken.
Die Methode kommt ursprünglich aus der Marktforschung und gibt einen Einblick in die Erwartungen, Bedürfnisse und Aversionen des Kunden. Es gibt eine Vielzahl von Möglichkeiten, die Informationen zu erfassen. Dazu zählen u.a. Focus Groups und Experteninterviews.
Die Vorteile der VoC-Methode im Überblick:
– bildet ein detailliertes Verständnis der Kundenanforderungen
– dient als gemeinsame Grundlage und Sprache für das Projektteam
– wichtiger Input zum Design konkreter Produkt-/Projektspezifikationen
– kann als Ausgangspunkt für Projekt-, Produkt- und Prozessinnovationen dienen
Das „House of Quality“ als Tool des Quality Function Deployment kann dazu dienen, Kundenanforderungen in konkrete Leistungsspezifikationen und –merkmale zu überführen.nach oben
DMAIC
Der DMAIC-Prozess bildet den Kernprozess für Six-Sigma-Verbesserungen und wird für die Verbesserung von bestehenden Produkten und Prozessen verwendet. Er erstreckt sich von der Definition (Define) von beispielsweise Kundenbedürfnissen über die entsprechende Datenerhebung (Measure) und der Analyse (Analyze) der Daten z.B. im Hinblick auf mögliche Ursachen für Abweichungen von definierten Leistungszielen über die Implementierung von Verbesserungen (Improve) bis hin zur Kontrolle (Control) der umgesetzten Maßnahmen.
Der DMAIC-Prozess fasst verschiedene Vorgehensweisen und Methoden zu einem systematischen Ansatz zusammen. Im Vergleich zum PDCA (Plan-Do-Check-Act) – Prozess, bei dem die Arbeitsschritte stärker ineinander verschachtelt sind, bietet der DMAIC-Prozess ein etwas übersichtlicheres aber vor allem rein sequentielles Projektablaufschema. Dies bedeutet, dass PDCA eine grundsätzliche Orientierung für Prozessverbesserung liefert, während DMAIC ein konkretes Ablaufmodell zur Optimierung bestehender Prozess nach der Six-Sigma-Methodik bietet.nach oben
Brainstorming
Brainstorming ist eine weiterentwickelte Methode zur Ideenfindung. Ursprünglich vor allem in der Werbung und als Kreativitätsverfahren eingesetzt, hat die von Alex F. Osborn bereits 1939 entwickelte Methode längst den Weg in viele andere Gebiete gefunden – so auch in der Produktentwicklung oder der Konstruktion neuer technischer Geräte.
Auch wenn der Begriff heute für eine Vielzahl verschiedener Techniken synonym verwendet wird, ist der Ablauf üblicherweise gleich geblieben. In einer kleinen Gruppe (idealerweise 5-7 Personen) sollen die Teilnehmer spontan Ideen zur Lösung eines Problems finden. Der Gedankenfluss der Teilnehmer soll dabei nicht unterbrochen werden, sodass jeder Gedanke erst einmal ungefiltert erfasst wird. Im Idealfall inspirieren sich die Teilnehmer gegenseitig und lassen die Ideen der anderen in den eigenen Lösungsansatz einfließen. Die Ideen und Ansätze werden festgehalten und protokolliert, sodass diese im zweiten Schritt analysiert und bewertet werden können.
Wichtig ist, dass die Gruppe in eine möglichst produktive und erfindungsreiche Stimmung versetzt wird. Daher gelten im ersten Schritt folgende Regeln:
Keine Kritik an anderen Beiträgen: Kreative Ideen können sich auch aus zunächst unsinnig erscheinenden Vorschlägen entwickeln.
Keine Wertung oder Beurteilung: Es sollen keine Hemmnisse entstehen, die den freien Gedankenfluss der Teilnehmer beeinflussen und stören könnten. Zur Beurteilung der Ansätze ist die zweite Phase da.
Jeder soll seine Gedanken frei äußern können.
Keine Totschlagargumente.
Je kühner und phantasievoller, desto besser: Ziel ist es, den Horizont zu erweitern und sich von alten Denkweisen zu lösen.
Im Rahmen eines Six Sigma-Projektes kann Brainstorming beispielsweise genutzt werden, um alle Aspekte eines Prozesses zu erfassen und so ein SIPOC-Diagramm mit Inhalt zu füllen.nach oben
SIPOC
SIPOC ist eine weit verbreitete Methode zur Visulisierung von Prozessen. Damit stellt es eine Form der „Momentaufnahme“ von Prozessen dar und dient als Ausgangspunkt für Verbesserungsmaßnahmen.
Supplier – Inputs – Process – Outputs – Customers
Die SIPOC-Methode dient vor allem dazu, sich relativ schnell einen Überblick über alle Elemente und Einflussgrößen des betrachteten Prozesses zu verschaffen. Für jeden Prozess sollen alle notwendigen Inputs und dazugehörige Outputs aufgeschlüsselt werden. Außerdem sieht die Methode vor, sowohl alle internen und/oder externen Inputlieferanten (Supplier), als auch alle internen wie externen Kunden (Customer) eines oder mehrerer Prozesse aufzuzeigen.
Die Vorgehensweise, jede Spalte eines SIPOC-Diagramms mit Inhalt zu füllen, kann dabei recht unterschiedlich ausfallen. Es kann durchaus Sinn machen, streng methodisch vor zu gehen und die Spalten von links nach rechts mit Inhalt zu füllen. Andersherum kann aber auch ein Brainstorming-Ansatz gewählt werden, der keine Einschränkung bezüglich des methodischen Vorgehens vorsieht und den Gedanken der Teilnehmer zunächst „freien Lauf“ lässt.
SIPOC ist ein sehr einfaches aber auch überaus effektives Verfahren. Es bildet nicht nur Prozessabläufe übersichtlich ab, sondern kann auch als Ausgangspunkt für detailliertere Analysen verwendet werden. Vor allem aber kann SIPOC genutzt werden, eine einheitliche Diskussionsgrundlage bilden, wenn es im Zuge eines Six-Sigma-Projektes darum geht, Prozesse im Team zu analysieren und zu verbessern.nach oben
ISO-Zertifizierungen im internationalen Vergleich
Prozessmanagement befasst sich mit der Analyse von Prozessen. In diesem Zusammenhang stellen ISO-Zertifizierung einen einheitlichen Standard dar, der Prozesse im Qualitätsmanagement entsprechen sollen.
Dabei sind ISO-Zertifizierungen im internationalen Vergleich unterschiedlich stark verbreitet:
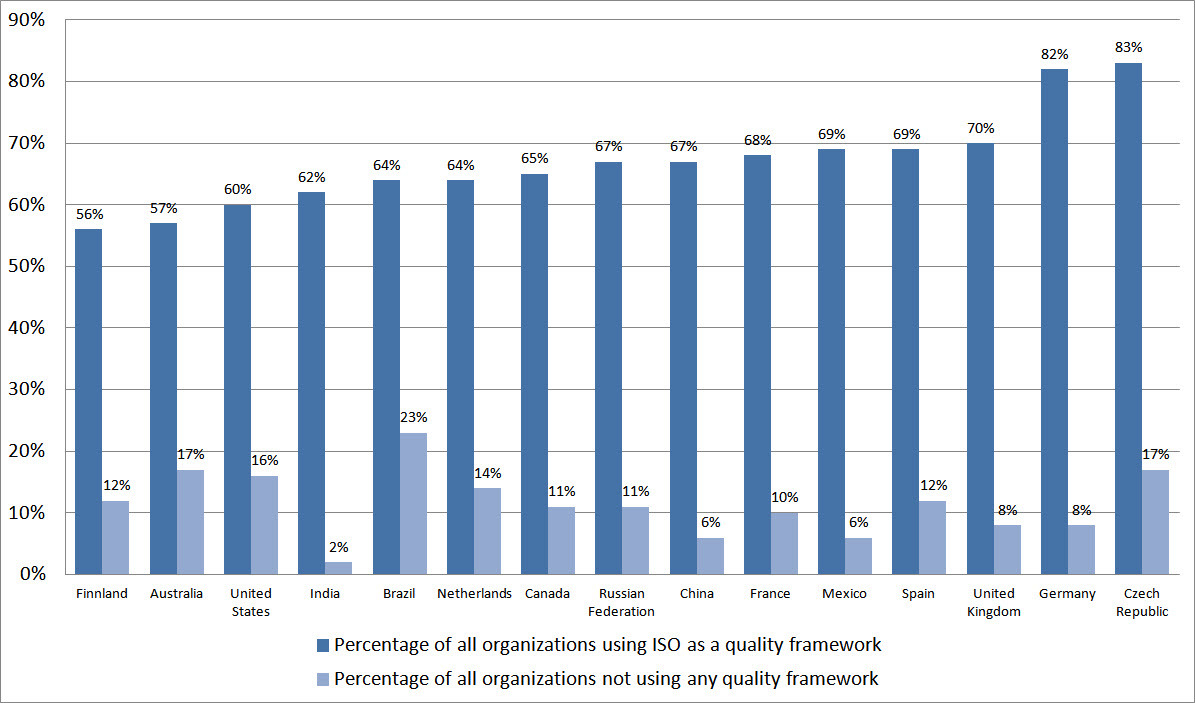
Quelle: The ASQ Global State Of Quality Discoveries 2013